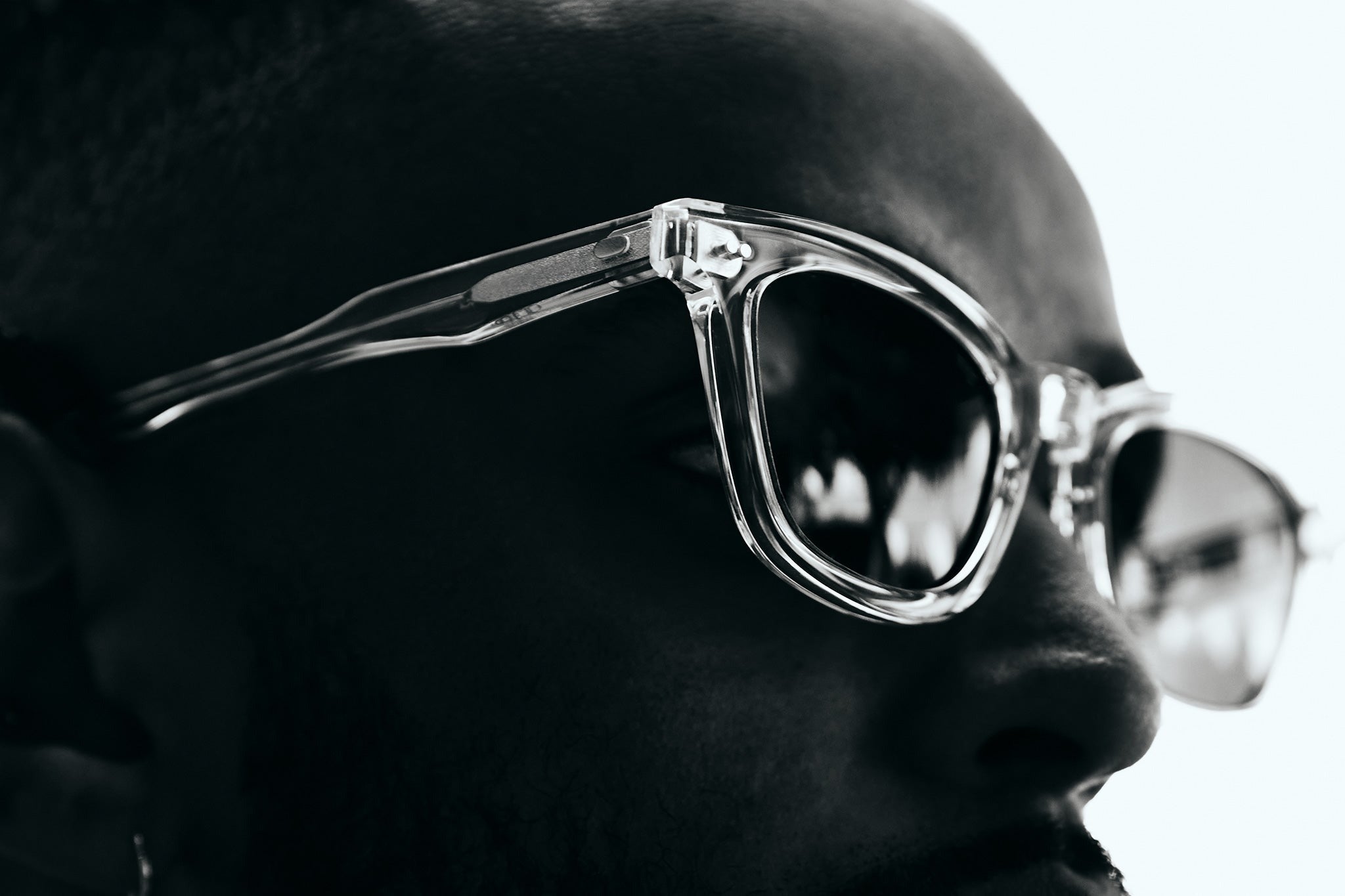
Our story
Drypond, a contemporary eyewear company based in Vancouver, British Columbia, embraces a second-generation approach to modern eyewear. Founded by Aidan Cheung in 2021, with roots connecting Shenzhen and Hong Kong, Drypond draws inspiration from vintage frames across Europe and America. Each meticulously crafted frame is produced from start to finish by a family-owned factory with nearly half a century of expertise in eyewear manufacturing. Using sleek Italian acetate, every style offers a thoughtful reinterpretation of retro frames favored by historically influential figures.
Drypond is a representation of family and legacy — an ongoing dialogue between generations. The brand believes in the importance of craftsmanship, artisanal products and voice of culture. When choosing priorities, Drypond is persistent in the mechanical world while adapting to innovation and design. With full focus on what is present and abundantly available, Drypond denies the need to predict future trends.
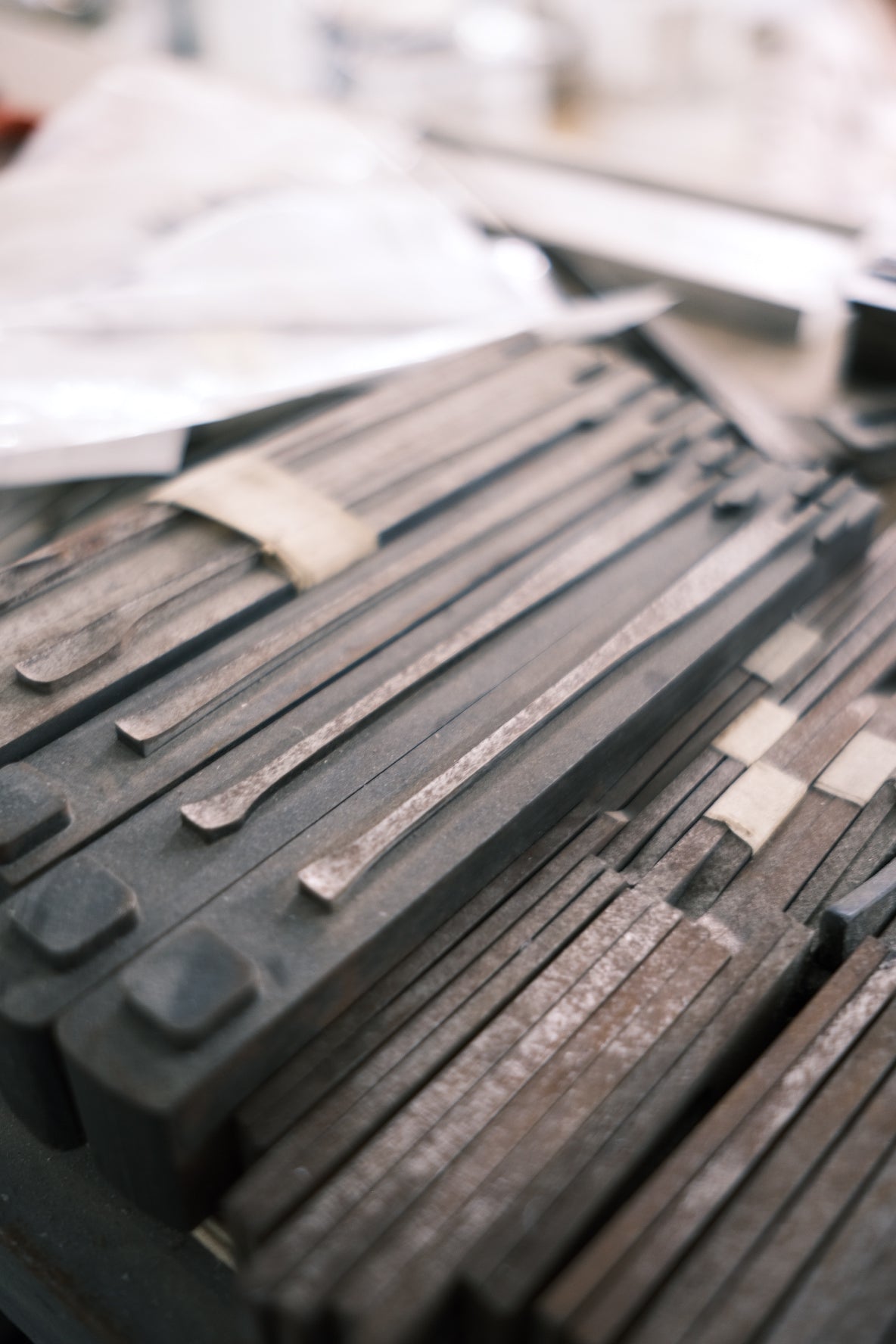
DESIGN
The earliest stages are prototyping and material selection, fine-tuning the frame’s design and select from exclusive supplies of materials like acetate.
The key is to come up with designs that make the user require a little courage when making their purchase.
PROCESS
To deliver the quality that luxury eyewear brands demand, our work is done by hand by craft experts that know what they’re doing. They are cut by hand, polished by hand, and inspected for defaults by hand. To put it frankly, if you want the look and feel of a premium frame, handmade is the place to start.
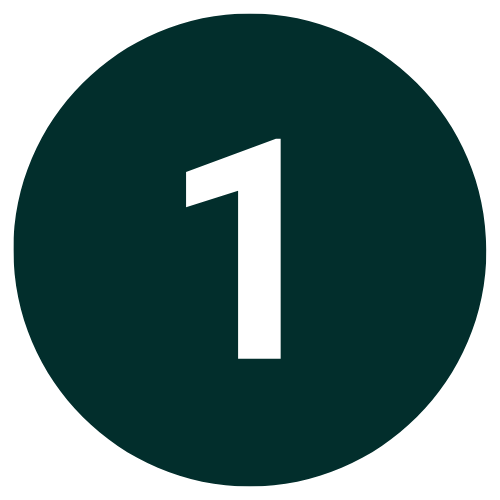
Cutting
Using 3-Dimensional imaging, the internal and external forms are cut out with routing machines
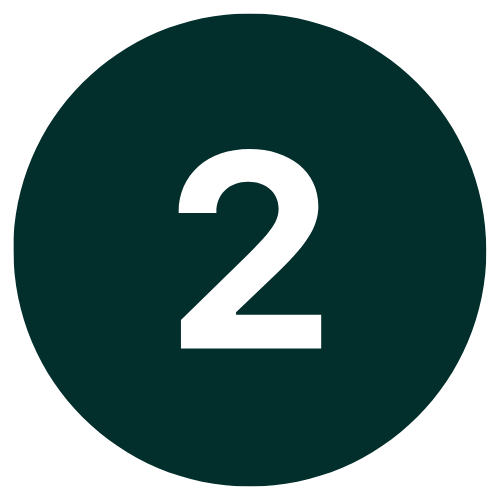
Curving
A frame is then set in a metal mold and heated at 80 degrees Celcius to create a curve. Pressing techniques are applied to correspond to each curve in the mold.
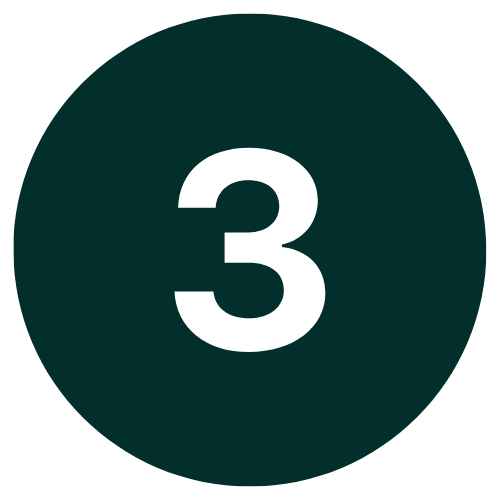
Sanding
Upon establishing the curves, experts apply the shape by rounding and edging methods to deliver the frame’s handcraft details of evenness.
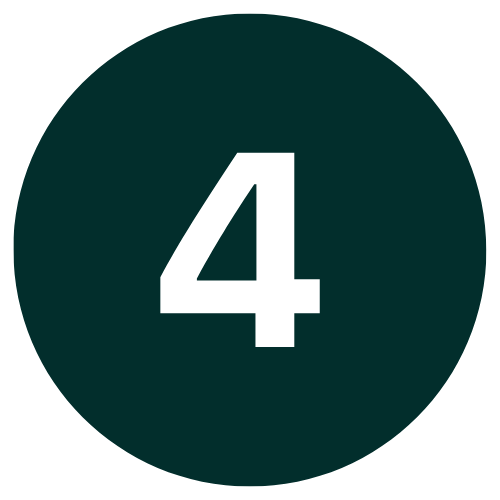
Buffing
Extending the handcraft aspects is the three stage polishing from matte, high gloss, to finer refinements. Each stage utilizes quality bases such as punice powder or Menzerna GW16 polish paste and could take 12 to 24 hours to process.
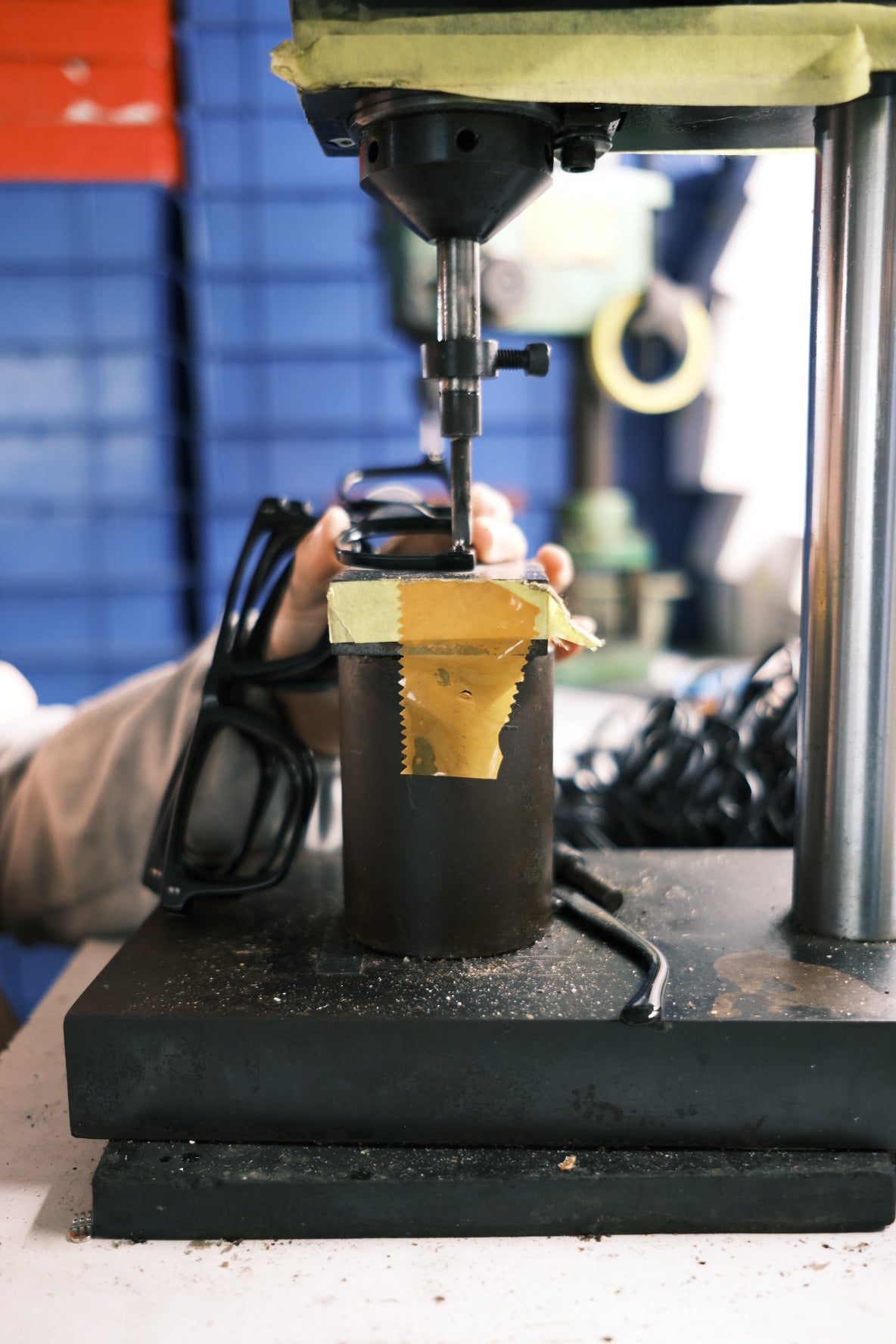
ASSEMBLY
With meticulous attention to detail, each piece is assembled to adjust the frames to fittings to complete the specifications with discrepancies less than 0.02mm
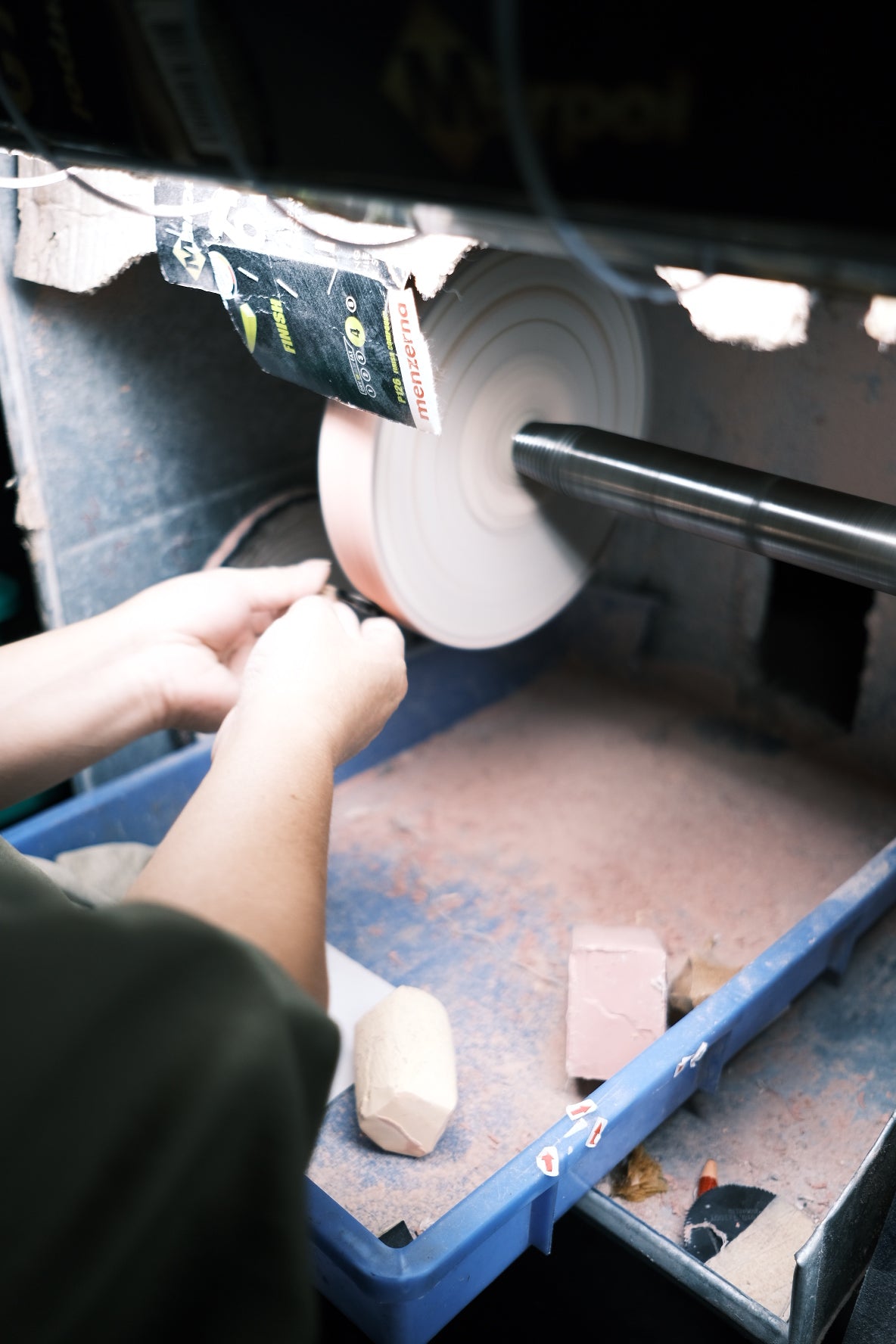
FINISHING
Any defects and misalignments are dismissed to ensure that the final product is presented with precision and original intention. Although individual craftsmen engage in different processes, Drypond’s quality check and control result in superior quality providing maximum comfort and durability.